Quality
what makes a project successful
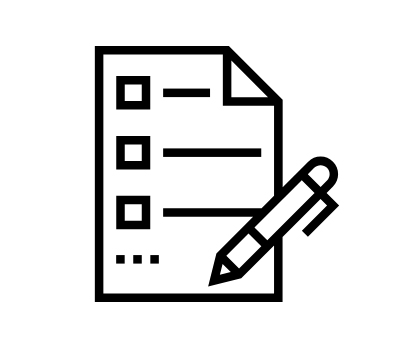
the concept of a project is its foundation
The concept of a project determines all aspects such as the surrounding conditions of a production plant, the battery limits and delivery splits, the final product qualities, all applicable engineering standards and a number of detail studies. Sufficient time is required for this important project phase.
more...
detail studies include
the integration of the process control and electrical systems into the existing structures
the applicable design standards (including their allowable exceptions for proprietary equipment items)
environmental and safety studies
a detailed future expansion planning
All these conceptual studies should be done as early as possible, because any alteration in the design has an exponential effect on the cost in a project.
Unfortunately many projects are in a hurry as soon as sales negotiations are completed and the project has been officially declared effective.
examples:
Any change from european or american engineering standards to a local national or company standard may have an major impact on cost and the project time schedule as the required stamps may not be available or existing designs and documents may have to be completely reworked.
All feedstock must be properly specified, any omission can have very serious consequences because the final product quality may not be reached or additional waste treatment unit may be needed. Especially if feedstocks are taken from natural resources or customers own facilities this needs to be reviewed with utmost diligence.
A simple connection flange for future expansion at one of the main cooling water headers may safe a huge amount of efforts later which could be a complete production stop (with loss of product), system draining, scaffolding, welding procedures, cleaning and restart – if only an additional chiller needs to be connected.
Especially if the project budget is tight the risk of under-designing some key equipment (e.g. if it is not matching the capacity in all phases of the production under its variable process conditions during commissioning) may rise. However, the cost of replacing such equipment later at site if the customer does not agree with any other compensation (i.e. normal practice in countries like Saudi Arabia) are by far higher, not to mention the additional site cost caused by the delay of the discussions with project managemnt, the redesign of the equipment, the delivery time of the new parts and the efforts for replacement (to hire a new erection contractor and wait for a regular production shut down).
The fire fighting concept of a chemical plant may have an impact on the design of a tank farm. It must therefore be done as early as possible and not at the end of a project to obtain the relevant approvals by the governmental inspectors.
A primary cooling water circuit with harbor water (i.e. an undetermined, variable composition of waters from the sea, a river and chemicals from surrounding facilities) requires a special design against corrosion and fouling of the whole unit, such as e.g. special titanium plate heat exchangers or additional inhibitor dosing units.
Operational convenience issues are recommended to be discussed before the projects is greenlighted. Which valve and which sight glass at a reactor requires an operational platform or for which equipment (agitators, motors) should have a permanently installed hoist for easy maintenance?
It is also very much recommended to clarify in the beginning of a project if there are any “unusual design conditions” such as
a sand storm proof design requirement for motors or sample points or
temperatures above 50 deg C in places like Saudi Arabia which may cause positioners of control valves to fail or require to reclassify the flammability of a process liquid
freezing temperatures in places like Sibiria, which may not allow erection works for several months per year
instable electrical power supply conditions at the location of the plant, which may require a detailed study for power failures during production
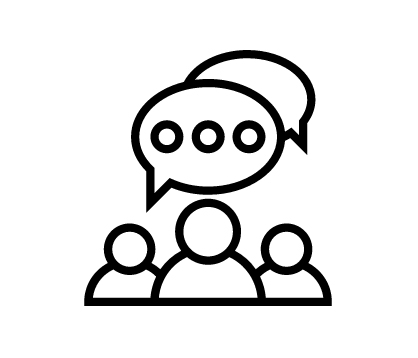
the project team needs to work very closely together
The cooperation of the project team members determines if the project can be completed in time. It is therefore essential for any project to carefully choose the team members.
more...
In most projects the team members are nominated by the engineering contractor based on availabilities in the departments and other personal factors. Until today it is not the normal practice that the customer retains the right to assess the project team by himself.
However, this does not guarantee the success of a project, as these team members may not know each other or may not be qualified enough.
From project management side all team members should be experienced, dedicated, cooperative and loyal. The project manager controls his project by agreeing to these nominations.
The engineering manager (technical project management) must be able to motivate the team, which he represents and defends against customers demands. He must know how to negotiate professionally and how to judge the quality of the documents (of all divisions).
Under all circumstances, “distributed” teams should be avoided. Close cooperation happens if teams sit together in one place, fitted with some resting areas for small talks and sufficient space for overview plans. In most cases, the distribution of the project team to different locations (or even different countries) is to be paid with costly meetings, special IT structures, email (mis)communication and a loss of management control.
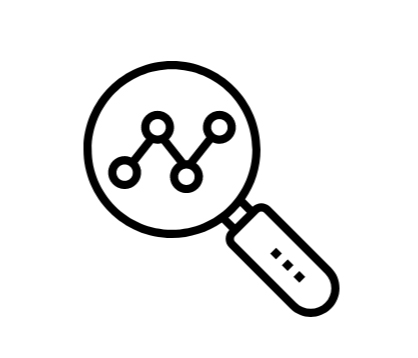
project control during execution ensures that the project stays on track
Professional project control detects small deviations early in the beginning and can tell if a project is leaving the track towards longer execution time or higher cost. This enables the management to counteract as long as this is still possible.
more...
Even though controlers may be under suspicion to “disturb” the project by asking too many questions while the team is working under pressure, their reports and observations are essential for the control of the project. This is because they collect the information of the experienced colleagues (who know of course exactly what the status of their work is, but – as human nature is – may not communicate all deficiencies unless somebody is looking at it) to generate an overall picture.
In addition to that, regular technical review meetings are essential for a proper project control. By means of 3D visualization, design deficiencies can be detected before the plant is built. It is one of the best cost saving activities of the whole project, because any alteration of the design at site costs a multiple of the original design.
Last but not least, a dedicated claims management can save a lot of money. It should be part of every bigger project.